Every year fires and ruptures in scuba, rebreather and oxygen cylinders occur. These incidents destroy property and injure, maim and even cause the death of cylinder filling-station operators as well as divers and innocent bystanders.
The safety of high-pressure gas cylinders is a primary focus of regulatory authorities in all countries. The U.S. Occupational Safety and Health Administration (OSHA) and equivalent governmental agencies in other countries define all highly pressurized containers as hazardous material (hazmat) or their country’s equivalent designation. These regulations mean that cylinder inspectors must have formal function-specific training.
Awareness, education and prudent actions by refilling stations and users can help prevent an accident that becomes one of the unfortunate statistics.
Cylinder Standards and Safety
The U.S. Department of Transportation (DOT), Transport Canada (TC) and the International Organization for Standardization (ISO) require cylinders to be designed, manufactured, inspected and certified to exacting engineering standards. Countries may have additional regulations regarding the competence of anyone handling cylinders. These standards and regulatory documents provide safety margins for cylinders to ensure decades of safe service for cylinders used within the intended conditions. The beverage industry, for example, safely uses high-pressure cylinders that are more than 70 years old.
The user must operate the cylinder within the design parameters, such as filling only to the rated service pressure and having cylinders inspected by formally trained and qualified technicians and requalified by a reputable, recognized test facility. More than 90 percent of ruptures occur during filling, so diligent inspection during this process is critical. Cylinders should operate safely throughout their entire service lives if users adhere to design and operating conditions.
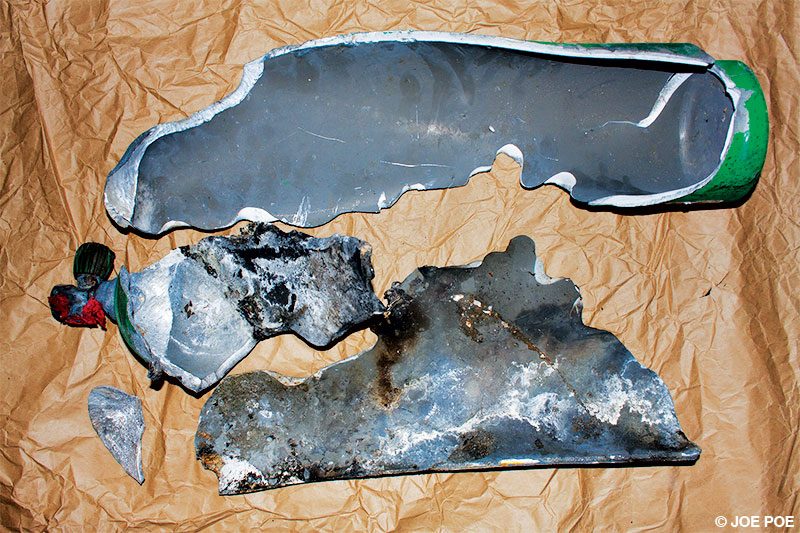
Why Cylinders Rupture
We can rarely guarantee that a cylinder has not been subject to overfilling, physical abuse or inadequate inspection. When cylinders are used well beyond their allowable stress limits, the potential for failure rises significantly. Regular overfilling close to or exceeding the hydrostatic test pressure will eventually cause deformation and lead to the cylinder’s inability to withstand even the allowable working pressure.
Exposing overfilled cylinders to high levels of heat — such as in the trunk of a car, which in some places can reach 200°F (94°C) in the summer — significantly increases the internal pressure. Aluminum cylinders are particularly susceptible to metallurgical changes when exposed to temperatures greater than 140°F (60°C) over a long time, which can result in structural damage to the metal.
Internal cylinder corrosion combined with a lack of mandatory internal visual inspections can eventually lead to inadequate wall thickness and rupture. Cylinders that are not suitably clean or fitted with inappropriate valves and filled with oxygen-enriched breathing gas can explode due to internal fire. The consensus of international standards is that oxygen-enriched gas contains more than 25 percent oxygen. It is important to note that cylinders do not always fail, even with dirty and inappropriate equipment. The technical specifications, however, indicate that fire is likely with the occurrence of one of several ignition causes — many of which are not apparent to the average user.
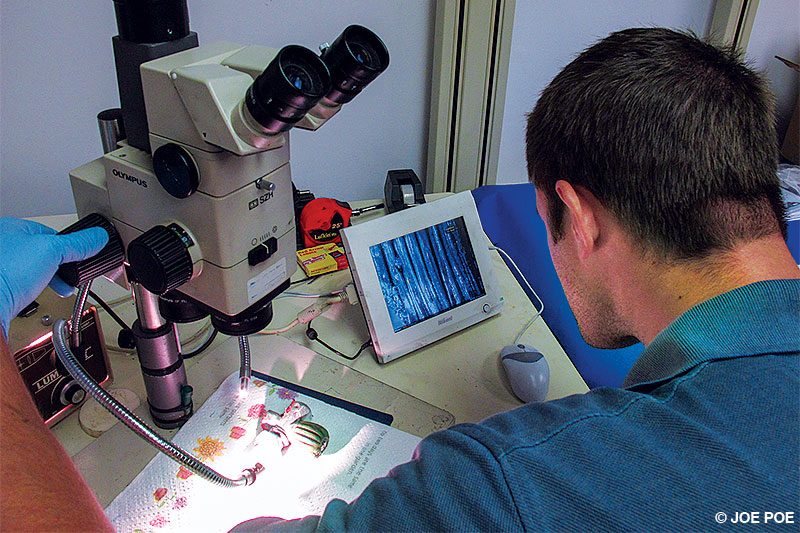
Mechanical damage to the outside of the cylinder is easier to visualize. Damage due to the incorrect matching of cylinder and valve threaded connections is much harder to see and has caused several devastating accidents.
The average scuba cylinder contains more than 1 million foot-pounds force, which correlates to the kinetic energy of a 3-ton truck traveling at 70 mph. The potential release of this amount of energy in a cylinder rupture demands that users have a thorough understanding of how to safely handle a cylinder.
Ensuring a Safe Cylinder
A few easy steps can collectively reduce your chance of being a statistic to infinitesimally small. One key step is to ensure that cylinder inspection and testing follows national or local regulations.
After each dive, purge cylinders after removing the regulator set to prevent trapping moisture in the valve so it doesn’t blow into the cylinder at the next fill.
Purge filling whips before each fill, especially if they are stowed in a way that moisture can enter and accumulate, such as in humid environments. Storing whips with the outlet facing down will help prevent any dirt particles from entering the cylinder, which otherwise could cause erosion or even ignition in oxygen-enriched applications.
To help the metal maintain its strength, store cylinders in a cool, dry place that prevents contact with any direct heat source. Store cylinders that will not be used for 90 days or longer almost empty — at around the first reading on the pressure gauge, which is typically between 100 and 200 psi (10 and 20 bar). Keep them upright in a secured position with the valve fully closed.
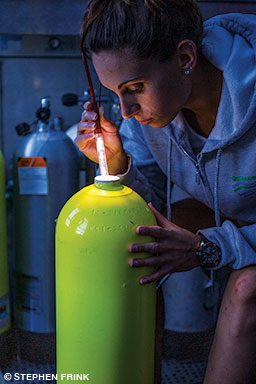
Examine cylinders for any signs of mechanical damage, such as dents or gouges, or evidence of valve damage caused by rough usage or less-informed divers. Ruptures rarely occur from cylinders being dropped or knocked over, but valve damage is often the cause of injuries or fatalities.
Do not use a cylinder if you observe any corrosion or noticeable mechanical damage, have a reason to suspect inadequate or missing mandatory inspections or the cylinder valve appears contaminated with any lubricant with an odor. If it is a rental, return it to the store; if it is yours, take it to a trained inspector regardless of the date on the visual inspection sticker.
Make sure you slowly and carefully open cylinder valves for both oxygen and any nitrox mixture. A sticky valve can present a challenge and requires urgent attention.
Maintaining your cylinders as required and questioning any possible issues you observe will add a level of safety. Add another level by having trained operators perform informal inspections during filling. A proper visual inspection and requalification by formally trained inspectors add a final level of safety. Accidents are the accumulation of many failures; safety is the accumulation of many layers of diligence.
Francois Burman is DAN’s director of risk mitigation. Mark Gresham is president and CEO of PSI-PCI, an agency that trains cylinder inspectors.
© Alert Diver — Q1 2021