EQUIPMENT
REPAIR
WORKSHOP
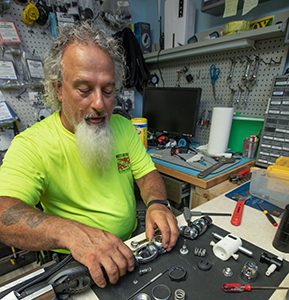
LIFE-SUPPORT DIVING EQUIPMENT must be kept in a good state of repair, be adjusted correctly, and be regularly maintained to reduce the likelihood of its failure during use. If you wish to do this yourself and establish a dedicated workshop there are several key safety factors you must consider.
You are responsible for the safety of your staff as well as the safety of the divers who use this equipment. Here are some key risks to pay attention to.
ASSESS THE ESSENTIAL
WORKING CONDITIONS
A clean and orderly workspace will go a long way to eliminating mistakes and will prevent contamination of components such as oxygen cylinders that must be kept clean. Similarly, inadequate lighting can compromise the integrity of serviced items and may lead to eyestrain or injuries to technicians. The guide provides information about suitable lighting levels for a range of workshop activities.
Poorly ventilated environments reduce staff members’ ability to concentrate, and hot and humid environments promote deterioration of service items and corrosion of tools.
Asses the Use of Any
Hazardous Chemicals
Technicians often use cleaning chemicals to remove dirt and contamination. These may be toxic, corrosive, or flammable.
Obtaining and storing safety data sheets for all potentially hazardous materials, ensuring that safe handling procedures are in place, and providing suitable warning signs are essential in protecting staff and anyone else who has access to the workshop.
A thorough risk assessment of all hazardous materials is needed to provide technicians with essential PPE required for eye, breathing, hearing, skin, and even foot protection. Be sure to issue and implement the use of PPE, provide training, and monitor the use thereof — failure by staff to use protection equipment provided to them may still result in liability problems should you not bring them to account when they fail to or elect not to use them.
Assess the Need for
Oxygen-Safety Procedures
Any servicing of equipment used with oxygen requires specialized knowledge to ensure safety — both in the workshop and when in use.
All that is required to cause a fire is a volatile fuel and a source of heat. Knowing which lubricants and sealing materials to use is critical in this regard.
You might believe that only very high levels of oxygen can support burning materials; however, our regulatory codes and safety standards regard any concentration greater than 23.5 percent, especially at pressures above 125 psi (0.9 MPa), as needing to be treated as pure oxygen.
Proper oxygen-cleaning requires thorough training, suitable tools, a clean workshop area, and the appropriate inspection equipment.
PAY ATTENTION TO
WORKSHOP LOGS
If it doesn’t exist in writing, it doesn’t exist. People often find themselves unable to provide any proof of what was done, by whom, and when. Assuring customers of proper servicing and being able to trace components and work performed will help you maintain your reputation as an excellent repair center.
Remember to maintain records of client complaints and failure reports. While you might assume these could be used as evidence against you, presenting them will make your case easier to defend.
Digitizing documents is helpful in protecting against loss or damage of paper records, and digital records are generally easier to retrieve and regarded as more credible.
DAN Customer Service
Mon–Fri, 8:30 a.m. – 5 p.m. ET
+1 (919) 684-2948
+1 (800) 446-2671
Fax: +1 (919) 490-6630
Email: Member@DAN.org
24/7 Emergency Hotline
In event of a dive accident or injury, call local EMS first, then call DAN.
24/7 Emergency Hotline:
+1 (919) 684-9111
(Collect calls accepted)
DAN must arrange transportation for covered emergency medical evacuation fees to be paid.
Medical Information Line
Get answers to your nonemergency health and diving questions.
Mon–Fri, 8:30 a.m. – 5 p.m. ET
+1 (919) 684-2948, Option 4
Online: Ask A Medic
(Allow 24-48 hours for a response.)