Some of mankind’s most amazing civil-engineering structures are underground tunnels and bridge foundations below the water table. During construction, the working spaces, or caissons, are pressurized with compressed air to keep out groundwater, and laborers (known as sandhogs) pass though pressure locks into and out of the caissons. In the 19th century, progress was rapid until the workers were afflicted with a mysterious condition called “caisson illness” when they returned to atmospheric pressure. The Brooklyn Bridge was completed before we learned how to prevent and treat the pain, paralysis and sometimes death due to what is now recognized as decompression sickness (DCS).
Caissons are dug vertically into bedrock to support bridge abutments, while tunnels are horizontal and used for roads, railroads, subways, water and sewage. Tunnels, formerly dug by gangs of sandhogs using picks, shovels and explosives, are now dug by tunnel boring machines (TBMs), which have giant rotating cylinder heads with toothed “faces” that cut through rock and muck as the TBM is forced along. In favorable rock formations, only the space in front of the TBM face is pressurized, and it’s only occupied for maintenance and replacing teeth. This limits pressure exposure and vastly improves safety.
Improved Tunneling Efficiency and Safety
When the 165-foot pressure limit for compressed air is exceeded, alternative gas mixes must be breathed to reduce the incidence of nitrogen narcosis, oxygen toxicity and DCS. TBMs can accomplish this with shorter working and decompression times. The foundation for these improvements was laid in the 1960s when deep diving and decompression research expanded in response to the need for offshore oil, particularly with the Organization of the Petroleum Exporting Countries (OPEC) oil embargo of the 1970s.
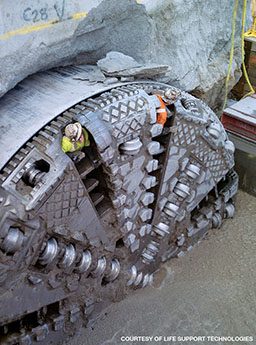
Saturation diving — in which divers remained at pressure for a day or more such that their bodies became equilibrated with the gas they breathed, and they could remain at depth without incurring additional decompression obligations — extended divers’ reach in depth and time to 1,000 feet of seawater (fsw) for weeks with few pressure-related injuries. Experience taught how heliox (helium-oxygen) and trimix (helium-nitrogen-oxygen) could be used at greater depths, how nitrox (nitrogen-oxygen) with more than 21 percent oxygen (oxygen-enriched air, or OEA) could be used at intermediate depths and how 100 percent oxygen could be used during shallow decompression. These techniques made for enormous improvements in productivity and safety.
Surface decompression (decanting) is another technique used widely in military and commercial diving to limit time in the water, where keeping warm is difficult. The diver remains at about 40 fsw before ascending to the surface in 1 minute, entering a deck decompression chamber (DDC), being pressurized back to 40 fsw in the DDC, breathing oxygen to clear inert gas and decompressing to the surface. Surface decompression is also useful in tunneling and caisson projects in which workers decant from an intermediate pressure of about 18 pounds per square inch gauge (psig) or 40 fsw, dress comfortably, enter a DDC and are repressurized to 18 pounds per square inch (psi) for decompression.
Another useful method developed in the 1960s and ’70s was saturation-excursion diving, in which divers lived in an underwater habitat or DDC and made excursions to greater depths and then returned (with or without decompression stops) to the saturation depth. Decompression to the surface was postponed to a later day. For deep excursion depths, trimix might be used as the breathing gas with careful monitoring of the oxygen exposure history to avoid oxygen toxicity.
Tunneling Around the World
The use of mixed gases for higher-intervention-pressure civil-engineering projects is more common in Europe and Asia than in the United States. Projects include deep shaft sinking at 4.8 bar (157 fsw) in the Netherlands, 5.8 bar (190 fsw) for subways in Russia and Seattle and 6.9 bar (225 fsw) in a Netherlands tunnel. The Western Scheldt tunnel project in the Netherlands used trimix at 4.8 bar (157 fsw) with saturation-excursion decompression. Mixed gases and higher intervention pressures have improved productivity with good safety records.
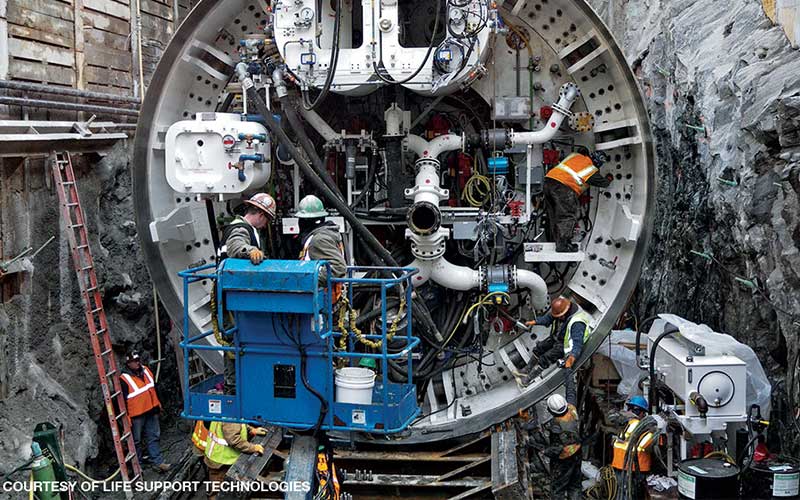
There are many demands for air-pressurized caisson systems in Japan, especially for very deep and long tunnels in which new magnetic levitation trains will run between Tokyo and Nagoya. Recently begun, this work will require 10 or more years with pneumatic caissons every 18 to 25 miles for vertical support shafts. Although remotely operated excavators will perform the vertical caisson work, engineers must go inside the air-pressurized caissons once every day or two to maintain machinery.
What Might Be Next in Tunnel Technology?
With the exception of mixed gases, deeper decompression tables intended for diving and a few saturation interventions, the caisson/tunnel industry in the United States has been reluctant to adopt the methods of deep diving technology that would likely improve intervention safety and productivity. Transferring these methods to tunnel work is technically and culturally challenging, because increased work time at higher pressures would require decompression times longer than the four hours under pressure permitted by existing union rules. But several new methods for improving tunnel construction are possible.
Constant oxygen partial pressure (PO2) decompression
Careful oxygen management during a hyperbaric exposure can help optimize decompression time. Commercial and military diving operations with heliox have taken advantage of higher PO2 levels while at pressure. During decompression, divers typically shift to air at a lower pressure and decompress on air thereafter. The PO2 at pressure, which is determined by the breathing equipment and length of the exposure, is typically 1.1–1.4 bar at pressure but, for fire safety, not greater than 21 percent by volume during decompression. If no additional oxygen is added, the PO2 will drop proportionally to the pressure, and more decompression will be required, which is a significant disadvantage. But by using rebreathing equipment, oxygen may be added continuously during decompression to arrive at an optimal PO2, usually above 1.0 bar.
The drawbacks of diving with rebreathers are requirements for multiple units, weight, awkwardness and accidental damage through “manhandling” within the lock or TBM. A hybrid approach would be to provide OEA (or mixed gas for deep dives) at pressure through an open-circuit mask or regulator mouthpiece. During decompression in the lock, workers would shift to a closed-circuit rebreather. A recirculating loop driven by a blower would condition the workers’ breathing gas (and the gas in the lock), remove carbon dioxide (CO2) and odors, maintain a constant PO2 and keep workers warm during decompression.
Replacing helium with crude neon
In 1972 scientists and engineers at Union Carbide’s Ocean Systems Inc. (OSI) perfected the use of neon as a replacement for helium in mid-range commercial diving to about 25 bar (815 fsw) and tested the concept in three open-water commercial dives to 640 fsw. Differences in decompression time between helium and neon were small, and a mixture of 33 percent neon (Ne), 33 percent helium (He) and 33 percent nitrogen (N2) appeared close to optimal for 160-250 fsw, with the oxygen (O2) percentage controlled during shallow decompression to avoid oxygen toxicity. Neon also has advantages over helium, including lower cost, warmer breathing gas, better drysuit thermal insulation and improved speech intelligibility.
As an economical alternative to the optimal mix, a lower grade of crude neon (50 percent Ne) containing N2 and O2 might be used without going through the costly scrubbing process to eliminate the other component gases that are needed anyway. Gas companies would tune their stacks to create an economical flow of crude neon in a range of about 50 percent Ne, 25 percent N2, 20 percent He and the balance O2 from the tail gas of their current “liquid air” distillation stacks. Once gas companies tuned their process for this economical mixture, special decompression tables would be developed.
Probabilistic decompression
Every dive profile has a finite DCS probability that can serve as a tool for comparing and selecting optimal decompression schedules. DCS probability also depends on factors such as thermal state and exercise that are very different between diving and compressed-air work. Understanding these effects will require further study based on recorded pressure-time profiles and DCS outcomes.
While there is no agreed-upon acceptable DCS probability, lower probabilities such as 0.025 percent are often considered appropriate for serious DCS such as paralysis, while 2 percent is more acceptable for joint pain. The lack of an absolute acceptable probability standard is addressed in the British concept of “as low as reasonably practicable” (ALARP). Since absolute elimination of DCS cannot be guaranteed, ALARP does not impose requirements that cannot be fulfilled, although preventive and protective actions appropriate to the risks are expected when possible.
Conclusion
Further progress in tunneling technology through the application of advancements in diving research may be achievable. How long this might take remains to be seen.
© Alert Diver — Q1 2017