“It seemed like a good idea at the time.” When I asked Divetech’s Nancy Easterbrook, project manager for the ex-USS Kittiwake, what possessed members of the Cayman Islands Tourism Association to embark on a decadelong ordeal to put this ship on the ocean floor, that was her facetious reply. Surely, neither she nor the other team members could have imagined the difficult scope of the project ahead of them. In retrospect, though, it was a very good idea, indeed.
I asked Nancy to reconstruct the timeline and hurdles faced to give divers a perspective on how a project like this unfolds.
In her words: The Kittiwake was the brainchild of the Cayman Islands Tourism Association to stimulate tourism. Cayman is a mature destination, one of the world’s first, going back more than 40 years. We have gorgeous walls and beautiful shallow reefs but not many really significant shipwrecks accessible to divers. Of course we have the wreck of the M.V. Keith Tibbetts on Cayman Brac, and that has been massively popular for the Brac and Little Cayman. But on Grand Cayman the Oro Verde has been pounded by wind and waves in the three decades it has been on the bottom, and the historical shipwreck Balboa is in the shipping lanes and hard to dive regularly. Grand Cayman needed a new shipwreck, and in 2002 we set about making a business plan to explore the possibility. With some government seed money in place and the confidence this was an attainable goal, we started shopping for a ship.
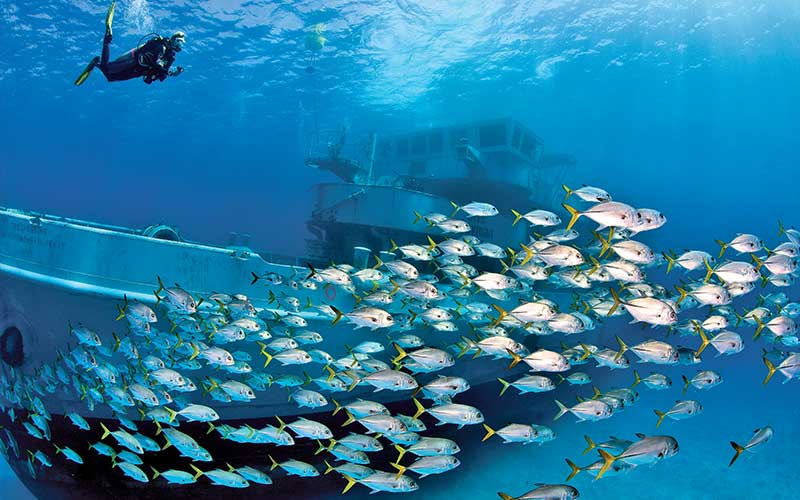
The U.S. Maritime Administration (MARAD) has the ships, for sure. In fact, they have three containment facilities for mothballed ships: one in California, one in Texas and probably the best-known collection of derelict military vessels moored on the James River in Virginia. These ships are kept afloat at significant expense to the U.S. government; if they sink unexpectedly, there is a huge environmental concern, so they have to be kept afloat until they can be scrapped or turned into an artificial reef.
Scrapping has to do with the value of the metal and materials onboard the ship, as a commodity, at any given time. Sometimes the scrap is not worth the expense to dismantle. Turning ships into artificial reefs is very expensive, certainly more than MARAD can undertake. Their position on this is that MARAD will provide a ship free of charge to a state or county that can prove the ship will be cleaned of all contaminants, safely towed and responsibly sunk at an approved site. Ours was to be a pilot project, the first ship donated to a foreign government.
It is not at all unusual for an artificial reef project to take a long time given the various government agencies that must approve every step along the way. Our project was no exception, and because of it, our goalposts tended to move as well, requiring us to be adaptable and in possession of unwavering resolve.
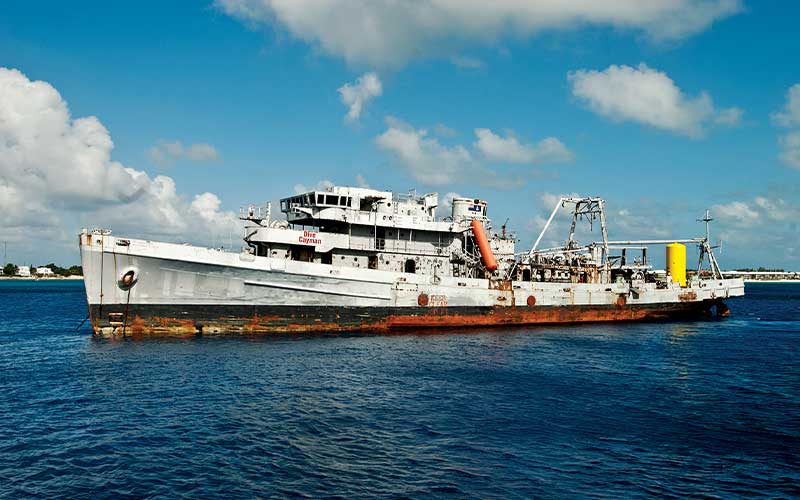
The one major variable that came into play was the result of a U.S. law known as the Toxic Substances Control Act, which in part mandates that when ships are donated for reefing, they have to be clean of all oils and contaminants such as asbestos and polychlorinated biphenyls (PCBs), a biohazard common to paint, wiring and many other bits and pieces of ships built at the end of World War II. The PCBs, in particular, were challenging. You never realize how many miles of wire have to be stripped and how many square yards of paint have to be chipped until you are obligated to remove them from a five-deck, 251-foot ship.
We were really lucky to find the Kittiwake, though. In addition to its classic profile, the ship was built with high-quality steel, fresh from the mill. The recycled steel was exhausted on other military ships built earlier for World War II, and only the best was left for the Kittiwake. This will help preserve the Kittiwake now that it is on our seafloor. We were also lucky the Cayman government was so supportive; month after month, year after year, they never lost their faith in this project.
We got title to the Kittiwake in August 2009, seven years after we wrote that first business plan. Many of our legal issues had to be resolved at the Cabinet level in Cayman, and in the United States there were Coast Guard, Environmental Protection Agency and other regulators to satisfy. On-island, we had to find exactly the right spot to sink the ship, and we had to do an environmental survey and prepare a sinking plan with input from marine architects. With so many stakeholder groups to satisfy and so many regulators providing oversight, this was a very high-profile project. The pressure was immense to make sure it all went exactly right.
Just when we thought we were nearing the end, we hit a delay from a small thing with a big effect. There are 32 seacocks on the Kittiwake. Those below the waterline were wired shut so the ship didn’t sink at the dock, yet each of them had a rubber gasket. The cumulative two pounds of rubber gaskets may or may not have had PCBs, but the only way to be sure was to replace them with PCB-free versions. But as the gaskets were underwater, the only way to replace them was to drydock the 2,200-ton ship.
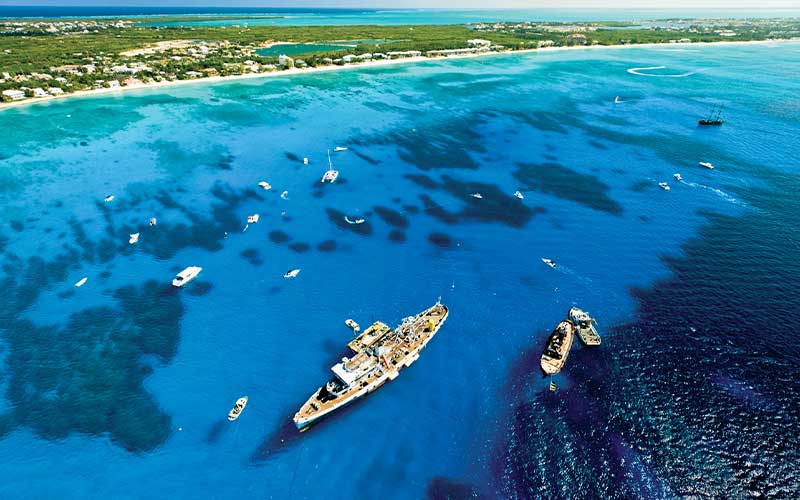
The question of the environmental impact of two pounds of rubber gaskets, even if they did contain PCBs, didn’t matter. We had to be in compliance. This alone cost the project an additional $40,000. Since this ship was for export and, therefore, under the purview of the Toxic Substances Control Act, we had to meet a higher standard than ships reefed in the United States. That high-standard requirement was OK with us as well as the Cayman Islands’ Department of Environment. As far as we were concerned, the cleaner the better.
But those kinds of unpredictable delays caused us to miss towing the ship in Spring 2010, and the insurance expense to tow during summer’s hurricane season was prohibitive. Finally, on Dec. 17, 2010, we had the nine-day weather window we needed to tow the Kittiwake from Norfolk, Va., to Grand Cayman’s George Town Harbor. On Dec. 25, we looked to the horizon and saw the Kittiwake being towed to its final duty station, the best Christmas present our local dive industry could possibly have had.
The ship spent three days in port so we could remove the paraphernalia needed for towing that was not part of the sinking plan, after which it was positioned off Seven Mile Beach with four 8-ton anchors with 2-inch chain to hold it in place. On Jan. 5, 2011, 10 years and 20 minutes after the inspiration first infected us, Grand Cayman had a world-class shipwreck to add to its dive portfolio. The Kittiwake now rests at the northern end of Seven Mile Beach, on the west (lee) side of Grand Cayman at latitude 19 21.714’N and longitude 081 24.073’W, just off the Sand Chute dive site.
Editor’s note: The Kittiwake is already an extraordinarily popular dive. With seven mooring buoys in place, it sits almost perfectly upright at a maximum depth of only 62 feet. The top of the wreck is within seven feet of the surface, making it one of the few intentional shipwrecks accessible to both scuba and even casual freedivers.
In the first month alone, 1,800 scuba tags and 1,100 snorkel tags were issued to access the wreck. The shipwreck is considered a private park, so there is an admission fee to build funds for maintenance, safety and environmental contingencies. Scuba-diving medallions cost US$10 per visit, a snorkel wristband US$5 and an annual pass is US$31.25.
© Alert Diver — Q2 Spring 2011